A Comprehensive Guide to the Refine and Advantages of Plastic Extrusion
In the large world of manufacturing, plastic extrusion arises as a extremely reliable and crucial procedure. Translating raw plastic into continual accounts, it caters to a wide variety of sectors with its remarkable adaptability. This overview aims to clarify the elaborate steps entailed in this technique, the kinds of plastic apt for extrusion, and the game-changing advantages it offers the market. The taking place conversation promises to unravel the real-world influences of this transformative process.
Comprehending the Essentials of Plastic Extrusion
While it might show up facility initially glance, the process of plastic extrusion is essentially straightforward - plastic extrusion. It is a high-volume production strategy in which raw plastic is thawed and formed right into a continual account. The process begins with the feeding of plastic product, in the kind of pellets, powders, or granules, into a heated barrel. The plastic is then thawed utilizing a mix of warm and shear, applied by a rotating screw. Once the molten plastic gets to the end of the barrel, it is forced through a small opening called a die, shaping it right into a desired type. The designed plastic is then cooled down, solidified, and reduced right into wanted lengths, finishing the procedure.
The Technical Refine of Plastic Extrusion Explained

Sorts Of Plastic Suitable for Extrusion
The selection of the ideal type of plastic is an important facet of the extrusion procedure. Numerous plastics use one-of-a-kind buildings, making them extra suited to specific applications. Polyethylene, for instance, is commonly used due to its affordable and easy formability. It uses superb resistance to chemicals and dampness, making it optimal for products like tubes and containers. Similarly, polypropylene is an additional preferred selection as a result of its high melting factor and resistance to exhaustion. For more robust applications, polystyrene and PVC (polyvinyl chloride) are frequently chosen for their strength and sturdiness. These are usual alternatives, the selection ultimately depends on the details needs of the product being produced. Comprehending these plastic kinds can substantially improve the extrusion procedure.
Contrasting Plastic Extrusion to Other Plastic Forming Approaches
Recognizing the types of plastic suitable for extrusion paves the way for a more comprehensive conversation on how plastic extrusion piles up versus various other plastic creating approaches. Plastic extrusion is unequaled when it comes to developing continual accounts, such as pipelines, seals, and gaskets. It also allows for a constant cross-section along the length of the product.
Key Advantages of Plastic Extrusion in Manufacturing
In the world of Going Here production, plastic extrusion supplies several considerable advantages. One remarkable benefit is the cost-effectiveness of the procedure, which makes it an economically attractive production method. In addition, this strategy gives remarkable product flexibility and enhanced manufacturing rate, consequently enhancing overall production efficiency.
Affordable Production Approach
Plastic extrusion jumps to the leading edge as an economical production approach in manufacturing. This procedure stands apart for its capacity to create high quantities of material swiftly and efficiently, providing suppliers with substantial cost savings. The main cost advantage is the ability to make use of cheaper basic materials. Extrusion utilizes thermoplastic products, which are less expensive contrasted to ceramics or metals. Better, the extrusion process itself is relatively basic, reducing labor expenses. In addition, plastic extrusion requires much less power than traditional manufacturing methods, adding to reduced operational prices. The process also reduces waste, as any type of defective or excess materials can be recycled and recycled, giving another layer of cost-effectiveness. In general, the financial advantages make plastic extrusion a highly appealing option in the production sector.
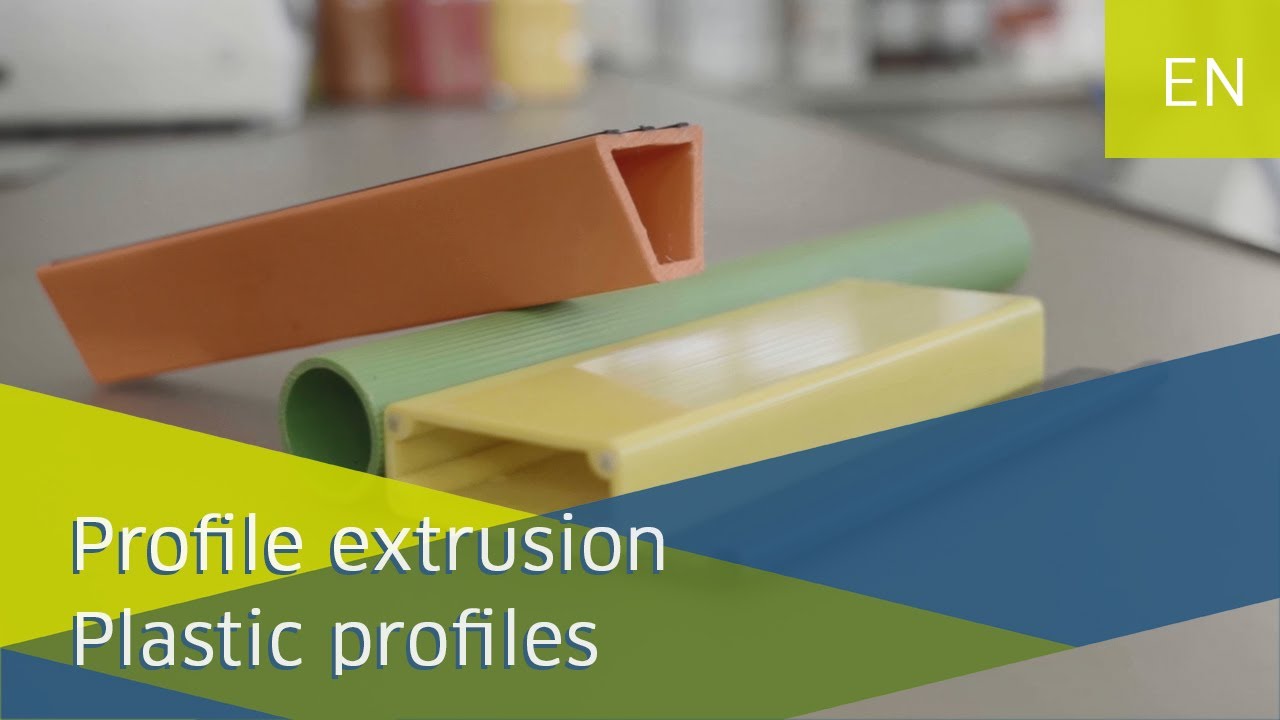
Superior Product Adaptability
Past the cost-effectiveness of plastic extrusion, an additional considerable advantage in manufacturing lies in its superior product versatility. This process allows for the production of a large selection of items with varying dimensions, designs, and forms, from basic plastic sheets to detailed profiles. The flexibility is connected to the extrusion pass away, which can be personalized to yield click this link the wanted product layout. This makes plastic extrusion a perfect solution for sectors that need tailored plastic elements, such as automotive, construction, and product packaging. The capacity to create diverse items is not only useful in meeting details market demands yet additionally in allowing makers to explore brand-new line of product with marginal funding financial investment. Fundamentally, plastic extrusion's item adaptability cultivates development while boosting functional efficiency.
Boosted Production Rate
A substantial advantage of plastic extrusion exists in its improved production speed. Couple of various other manufacturing procedures can match the speed of plastic extrusion. Additionally, the ability to keep constant high-speed manufacturing without sacrificing item high quality sets plastic extrusion apart from various other approaches.
Real-world Applications and Effects of Plastic Extrusion
In the realm of manufacturing, the strategy of plastic extrusion holds profound importance. The economic advantage of plastic extrusion, mainly its cost-effective and high-volume outcome, has actually changed manufacturing. The industry is persistently striving for developments in recyclable and naturally degradable products, showing a future where the advantages of plastic extrusion can be preserved without compromising environmental sustainability.
Conclusion
In conclusion, plastic extrusion is a reliable and very effective approach of changing resources into diverse products. It offers various benefits over various other plastic creating techniques, including cost-effectiveness, high outcome, very little waste, and design flexibility. Its you could look here influence is greatly really felt in different industries such as construction, auto, and durable goods, making it an essential process in today's production landscape.
Digging much deeper into the technical procedure of plastic extrusion, it begins with the option of the proper plastic material. As soon as cooled down, the plastic is cut right into the needed lengths or injury onto reels if the product is a plastic film or sheet - plastic extrusion. Contrasting Plastic Extrusion to Other Plastic Forming Approaches
Recognizing the types of plastic suitable for extrusion leads the way for a more comprehensive conversation on how plastic extrusion piles up against other plastic developing approaches. Few various other manufacturing procedures can match the rate of plastic extrusion.